Background to case study
Abbey Glass, based in South Wales, have provided a bespoke glass and glazing service for both commercial and domestic clients for over 20 years. Abbey Glass supply and fit curved glass, balustrades, mirrors and back painted glass as well as modular bathrooms for large commercial clients. Abbey have grown by around 20% per annum over the last five years and built partnerships with national brands including the Whitbread group, Premier Inn, Brewers Fayre, Table Table, Costa Coffee, Beefeater and many more. They have developed innovation in partnership with Premier Inn to deliver their ‘Good Night’s Sleep’ promise to their customers throughout the UK. Abbey are eager to continue to produce innovative products for their clients.
The innovation knowledge and skills of the innovation team at Abbey has been enhanced through the DIPFSCC programme. Angela, the Commercial Director and innovation team lead, has coordinated the development of the innovation team who are responsible for looking at existing challenges their customers present and developing new products to obtain new customers. Angela attended the programme to enhance her skills and knowledge around developing new products/service solutions and Circular Economy principles.
Impact of the programme
Angela talked through a few examples of where the tools introduced on the programme have been used to develop their new product development (NPD) internal processes. One example of where they have applied learning from the programme is on a project for a large hotel chain that required hundreds of painted glass screens and decorative pieces in a short space of time.
Using the process mapping skills developed on the programme Abbey discovered the bottleneck in their process was the drying time required for painted glass. The drying time of the ordered glass screens was causing issues with their customers and storage issues within the factory. The approximate production time for each piece was two days. With market research the innovation team at Abbey discovered that a machine was available that could reduce the production time of each piece to approximately two hours. The machine in question was very expensive and so the project referred Abbey to a Welsh Government innovation specialist who then supported Abbey to make an application to the SMART Cymru innovation fund. Abbey were successful with their application with the support of the innovation specialist.
The recently installed machine at Abbey’s factory in Porth and is proving to be a huge success. There are both economic and environmental benefits from the new production methods using the new machine. The production time has been reduced from two days to two hours, which has increased Abbey’s capacity to deliver to customers. The machine also uses less paint than their traditional method and so creating considerable environmental benefit. Secondly, Abbey are saving on the staff time, as fewer labour hours are required to produce a single piece. The new machine has also reduced their energy consumption as their traditional paint process used expensive extraction fans.
Angela advised: “We’ve got real value from the University innovation programme, we’re really pleased with the time, cost savings and positive environmental impact resulting from the new machine we were able to buy with Welsh Government support. The future impact will be huge as well. The tools and models I’ve picked up from the programme are being used by the innovation team in our monthly meetings, which bodes well for our future growth here at Abbey.”
Figure 1: New machine at Abbey Glass
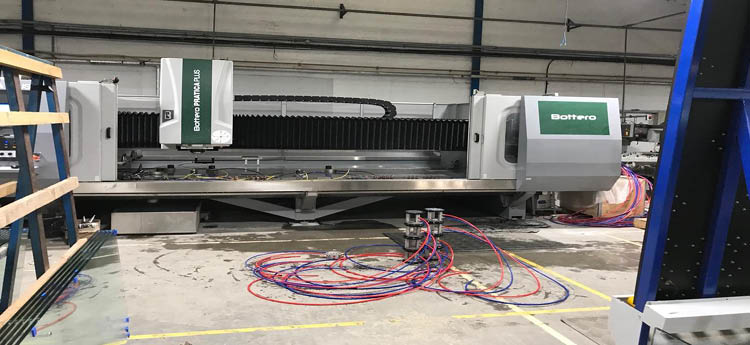