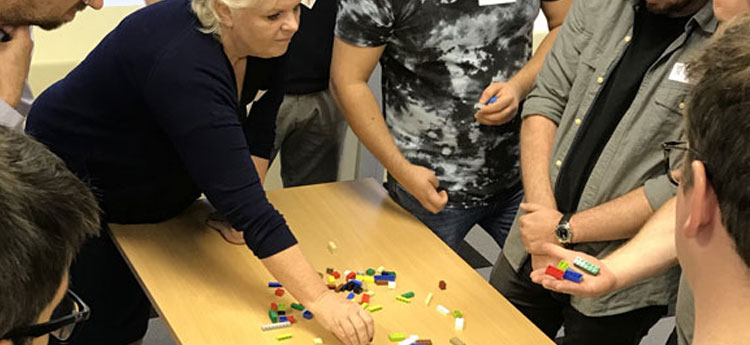
Swansea University’s School of Management is rolling out a project across Wales to support businesses through the product development process. The ‘Developing Innovation Performance of Firms and Supply Chain Clusters’ (DIPFSCC) programme helps businesses of any size to develop new products or services, and can also introduce businesses to funds that can support their new product or service development, including testing, industrial research and commercialisation.
The structured programme takes participants through the new product development process with other businesses in their supply chain, and across sectors, and develops the innovation management knowledge and skills of the individuals and firms involved.
The project is currently working with businesses including Ford Bridgend Engine Plant, Dwr Cymru Welsh Water, Abbey Glass, Treforest Glass and The Health Dispensary.
Gary Walpole, who specialises in leadership and management development, is leading the project. Gary said: “The programme is delivered through regular workshops and site visits, with the businesses using their new skills and knowledge to make changes at their workplace. In March, for example, participants from Dwr Cymru and Ford Bridgend Engine Plant came to the University and worked together in cross-sector teams to develop solutions to real-life challenges they are facing in their respective workplaces.”
The programme can also support businesses to apply for funds by introducing them to Welsh Government innovation specialists.
Case study - Ford Bridgend Engine Plant
The Ford Bridgend Engine Plant (BEP) is a major producer of engines supplying approximately 620,000 engines in 2017 to Ford for vehicles sold worldwide.
The Plant has recently enhanced its industry 4.0 capabilities (the automation and data exchange system currently used in manufacturing technologies) by establishing an innovation lab within the factory and developing their rapid prototyping capacity.
Phil Moreton is a Senior Development Engineer at BEP, leading on a number of new products for Ford. He attended the DIPFSCC programme to enhance his skills and knowledge of developing new products and service solutions and to find out more about the Circular Economy (CE).
Phil said: “We got real value from the tools and knowledge we picked up from the DIPFSCC programme. For example, we decided to apply the CE principles to the printing of plastic parts at the Plant, reviewing the plastic used by the 3D printers in the Ford factory. Our supplier was able to switch the printer feedstock from virgin to recycled plastic. This has had economic and environmental benefits with Ford now saving approximately £18 per kilo on the cost of their feedstock.”
Ford is also now exploring, with their supplier, how the plastic that comes into the factory as packaging can be recycled so that it can be used as 3D printer feedstock. This change will allow Ford BEP to ‘close the loop’ and reuse the plastic that comes into the plant.
To further apply CE principles and reduce costs, Phil and his team are now looking at cataloguing all the plastic parts held in the factory in order to begin 3D printing the parts onsite.
Phil said: “Being able to print our own parts will significantly reduce costs, reduce the time of delivery and allow us to reduce stock levels. The factory will be preventing hundreds of kilos of plastic waste going into landfill. There will also be considerable environmental savings stemming from reduced transport of parts to BEP from around the world.
“We’re really pleased with the cost savings and positive environmental impact resulting from the change to recycled plastic feedstock. The future impact will be huge, as we will exponentially increase the number of parts that we print within the factory. We’re just starting to see the environmental benefits and cost savings from our investment in industry 4.0 methods, which is really exciting for us here at BEP.”
If you would like to find out more about how the DIPFSCC programme can help your business, please contact our Business Engagement team.